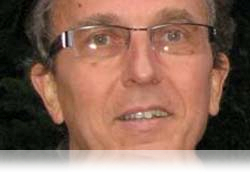
Michel Bruley, Directeur Marketing Teradata Europe de l’Ouest
Lorsque les premières unités sortent de la chaîne de montage pour être vendues, seules des comparaisons limitées peuvent être faites par rapport aux spécifications de performance de la base de test. Par conséquent, la fabrication teste puis expédie des produits à risque, et d’autant plus à risque si la base de test n’est pas reliée au système de gestion du cycle de vie des produits de l’entreprise.
Pour les entreprises manufacturières les données sur la performance des produits, les rendements, les plannings de livraison et une foule d'autres paramètres peuvent faire ou défaire le succès d’un lancement de produit, et finalement affecter sérieusement les résultats de l'entreprise elle-même. La question fondamentale n'est pas tant de savoir si les données sont disponibles, mais c'est le laps de temps entre l'obtention de l'information, la transformation en connaissance et les décisions de changement, par exemple des décisions de l’ingénierie avec la mise au point d’une nouvelle conception pour répondre aux problèmes, la définition de nouvelles normes de fabrication, etc.
Il est clair qu’il est hautement préférable d’être immédiatement précis, mais c’est très difficile pour les nombreuses organisations qui travaillent avec de multiples systèmes spécifiques à chaque département, car elles doivent commencer par échanger des données entre départements, pour pouvoir les analyser et avoir une vision globale. Plus il y a de systèmes différents, plus les nomenclatures ont tendance à diverger dans le temps, et donc plus ces entreprises rencontrent de multiples problèmes et de délais pour intégrer les données.
Si au lieu de rapprocher occasionnellement les données des différents départements, une entreprise dispose d’un système consolidant les silos dans une base unique, offrant une vue centralisée pour l'analyse, la gestion de la qualité des données est grandement facilitée, et les processus d’analyse peuvent être raccourcis de façon spectaculaire. Avec une telle architecture il est plus aisé de gérer un référentiel central commun, et de permettre des analyses rapides qui génèrent des connaissances opérationnelles immédiates et concrètes pour tous les départements.
Dans le cas d’un lancement de produit, si la vente, le service après-vente, la logistique, la fabrication, l’ingénierie etc., peuvent mieux partager et analyser leurs données, des réponses plus rapides et de meilleures solutions peuvent être trouvées pour fixer les problèmes, par exemple lorsqu’il s’agit de défauts de conception. Grâce à des indicateurs clés de performance de l’ensemble de la chaîne, des mesures appropriées peuvent être prises immédiatement. En outre, une plus grande variété d'analyse de données peut être effectuée pour générer des connaissances, l'efficacité opérationnelle s’en trouve améliorée et tout cela finit par impacter positivement les résultats financiers de l’entreprise.
Les résultats de terrain montrent que les entreprises manufacturières peuvent prendre des décisions opérationnelles de cinq à quinze fois plus rapidement grâce à la mise en œuvre d'un entrepôt d’entreprise. C’est ce qu’ont bien compris des entreprises comme 3M, Dell, Nokia, Daimler, Boeing, General Electric, Ford, Intel, Western Digital, Lucent, Good Year, Volvo, Unilever, etc. qui ont mis en place des solutions Teradata pour consolider leurs données dans un référentiel d’entreprise.
Pour aller plus loin, vous pouvez utilement consulter mes autres articles sur le sujet :
http://www.decideo.fr/bruley/Sortir-de-l-impasse-des-systemes-decisionnels-heterogenes-par-la-consolidation_a8.html
Pour les entreprises manufacturières les données sur la performance des produits, les rendements, les plannings de livraison et une foule d'autres paramètres peuvent faire ou défaire le succès d’un lancement de produit, et finalement affecter sérieusement les résultats de l'entreprise elle-même. La question fondamentale n'est pas tant de savoir si les données sont disponibles, mais c'est le laps de temps entre l'obtention de l'information, la transformation en connaissance et les décisions de changement, par exemple des décisions de l’ingénierie avec la mise au point d’une nouvelle conception pour répondre aux problèmes, la définition de nouvelles normes de fabrication, etc.
Il est clair qu’il est hautement préférable d’être immédiatement précis, mais c’est très difficile pour les nombreuses organisations qui travaillent avec de multiples systèmes spécifiques à chaque département, car elles doivent commencer par échanger des données entre départements, pour pouvoir les analyser et avoir une vision globale. Plus il y a de systèmes différents, plus les nomenclatures ont tendance à diverger dans le temps, et donc plus ces entreprises rencontrent de multiples problèmes et de délais pour intégrer les données.
Si au lieu de rapprocher occasionnellement les données des différents départements, une entreprise dispose d’un système consolidant les silos dans une base unique, offrant une vue centralisée pour l'analyse, la gestion de la qualité des données est grandement facilitée, et les processus d’analyse peuvent être raccourcis de façon spectaculaire. Avec une telle architecture il est plus aisé de gérer un référentiel central commun, et de permettre des analyses rapides qui génèrent des connaissances opérationnelles immédiates et concrètes pour tous les départements.
Dans le cas d’un lancement de produit, si la vente, le service après-vente, la logistique, la fabrication, l’ingénierie etc., peuvent mieux partager et analyser leurs données, des réponses plus rapides et de meilleures solutions peuvent être trouvées pour fixer les problèmes, par exemple lorsqu’il s’agit de défauts de conception. Grâce à des indicateurs clés de performance de l’ensemble de la chaîne, des mesures appropriées peuvent être prises immédiatement. En outre, une plus grande variété d'analyse de données peut être effectuée pour générer des connaissances, l'efficacité opérationnelle s’en trouve améliorée et tout cela finit par impacter positivement les résultats financiers de l’entreprise.
Les résultats de terrain montrent que les entreprises manufacturières peuvent prendre des décisions opérationnelles de cinq à quinze fois plus rapidement grâce à la mise en œuvre d'un entrepôt d’entreprise. C’est ce qu’ont bien compris des entreprises comme 3M, Dell, Nokia, Daimler, Boeing, General Electric, Ford, Intel, Western Digital, Lucent, Good Year, Volvo, Unilever, etc. qui ont mis en place des solutions Teradata pour consolider leurs données dans un référentiel d’entreprise.
Pour aller plus loin, vous pouvez utilement consulter mes autres articles sur le sujet :
http://www.decideo.fr/bruley/Sortir-de-l-impasse-des-systemes-decisionnels-heterogenes-par-la-consolidation_a8.html
Autres articles
-
Teradata lance des cas d’usage d’IA générative à démarrage rapide grâce à l’intégration d’Amazon Bedrock
-
Teradata nomme Louis Landry au poste de Chief Technology Officer
-
Teradata AI Unlimited pour Microsoft Fabric est désormais disponible en avant-première via Microsoft Fabric Workload Hub
-
Teradata facilite l’application concrète de l’IA générative et accélère la création de valeur pour les entreprises
-
Teradata propose des capacités d’IA exceptionnelles pour les grandes entreprises et les environnements hybrides en collaboration avec NVIDIA