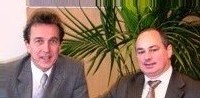
L’intelligence active concerne les décisions relatives à la chaîne de valeur, prises pour optimiser la conduite des opérations. Il s’agit de permettre aux opérationnels de fonder leurs décisions sur une vue holistique des informations de l’activité de l’entreprise. 85% des décideurs opérationnels disent souhaiter plus d’informations et 86% disent que l’information en « temps réel » est importante (le temps ‘réel’ étant relatif à l’activité elle-même, il peut se traduire par un délai s’évaluant en secondes, en minutes voire en heures). Pour répondre à ce besoin, le système d’information décisionnel gère de façon détaillée les événements opérationnels, sans délai de mise à jour par rapport aux systèmes opérationnels, et constitue un entrepôt de données d’entreprise ‘actif’, qui calcule des indicateurs clés au fil de l’eau ou à intervalles courts et assure le partage des informations utiles à une prise de décision cohérente aux différents postes opérationnels.
Les industries manufacturières offrent de nombreux exemples de processus et domaines d’application dans lesquels une telle intelligence active peut apporter des avantages significatifs pour la conduite des opérations, comme l’illustrent les quelques cas réels détaillés ci-dessous : gestion des commandes, de la prise d’ordre à la livraison ; planification de la demande ; optimisation des transports ; gestion des garanties ; gestion des pièces détachées ; consolidation et publication des résultats financiers.
Cas numéro 1 : Garantir une efficacité totale du processus allant de la prise de commandes à la livraison chez un fabricant d’articles de sport
Pour cela il fallait parvenir à accélérer les sous-processus et les flux de données associés tout au long de la chaîne du processus global, du centre d'appel, à la logistique, en passant par la fabrication. Le problème rencontré provenait de l’existence d’un ensemble de systèmes hétérogènes, plus ou moins intégrés, ce qui avait pour résultat un délai de six semaines de la commande à la livraison. La solution a consisté à mettre en place une base commune pour traiter l’ensemble des données nécessaires à la fois aux activités opérationnelles et décisionnelles. Cette architecture a permis de ramener de 6 semaines à 48 heures le traitement de 3000 commandes/jour, et d’optimiser dynamiquement les stocks et la production. Cette base de données satisfait près de 2 Millions de requêtes par jour, ceci incluant le suivi de la situation des commandes par les clients via le web.
Cas numéro 2 : Optimiser la planification de production en fonction de la demande
Les planifications type APS (Advanced Planning & Scheduling) sont établies de façon mensuelle ou hebdomadaire. Dans ces conditions, trop souvent les prévisions de production ne sont pas en phase avec la demande réelle, et au final il peut y avoir selon les produits trop ou pas assez de stock. Les difficultés habituelles viennent du manque de fraîcheur des données prises en compte à tous les niveaux de la chaîne, du délai de calcul des différents plans, qui aboutissent à un taux de 35% de prévisions erronées. La solution consiste à réaliser des Plans plus fréquents en s’appuyant à la fois sur des informations historiques des années antérieures et des données fraîches du jour de la situation réelle des commandes, des stocks, des livraisons, des plannings des promotions etc. Le système doit être à même de re-planifier en quelques heures, dés que des variations importantes se produisent, grâce à des pré-alertes sur les dérives par rapport aux plans. Dans les grandes entreprises l'amélioration du processus de planification met en jeu des millions d’euros en terme de réduction des stocks et de réduction des ventes perdues, sans compter l’accroissement de la satisfaction clients qui trouvent leurs produits en rayon ou sont livrés en temps et en heure.
Cas numéro 3 : Optimiser l’utilisation des capacités de transport
Une mauvaise utilisation des capacités de transport peut générer une perte financière non négligeable. Dans la plupart des cas, ces pertes sont liées à planification défectueuse de l’utilisation et du chargement des camions. Ces défauts de planification proviennent d’une qualité insuffisante des informations, d’un automatisation trop partielle des règles de rotation et chargement des camions, ou à une faiblesse des procédures. Dans tous les cas, la connaissance instantanée de la situation de chaque véhicule est nécessaire à l’optimisation des rotations, des trajets et des chargements. La solution consiste à automatiser les plans de chargement, et grâce à des données précises et détaillées permettant de disposer d’alertes en temps réel et de plans dynamiques, les chargeurs de dock maximisent l'utilisation de la capacité de leurs camions.
Cas numéro 4 : Limiter les réclamations frauduleuses en matière de garantie
Au niveau de la gestion des garanties les constructeurs d'automobiles veulent réduire la quantité de réclamations frauduleuses instruites et payées. L’un des principaux problèmes tient au fait que 85% des données de garantie se présentent sous la forme de textes non structurés et sont donc peu pris en compte dans le processus de décision. La solution consiste à intégrer dans un entrepôt de données d’entreprise les textes structurés ou non structurés avec les données opérationnelles et historiques, et à partir de cet ensemble et via des modélisations prédictives, traquer les réclamations frauduleuses. Ce dispositif permet d’être très réactif face aux nouvelles pratiques frauduleuses et de savoir les identifiées avant qu’elles ne prennent de l’ampleur. Une telle approche permet d’améliorer la rentabilité en faisant baisser significativement le coût des réclamations frauduleuses.
Cas numéro 5 : Améliorer la distribution de pièces détachées
Les clients sont insatisfaits quand les pièces détachées dont ils ont besoin ne sont pas disponibles, mais le stockage de pièces qui ne sont pas demandées coûte cher. En fait la satisfaction des clients dépend en grande partie de la connaissance en temps réel de l’état des stocks et des possibilités de livraison à travers la chaîne d'approvisionnement. Ainsi grâce à l’utilisation d’un entrepôt de données d’entreprise il est possible d’obtenir une visibilité de bout en bout de l’ensemble de la chaîne. Et de disposer de prévisions, et d’alertes proactives, ainsi que d’une gestion dynamique des priorités (par exemple quels camions décharger en premier) qui permettent une meilleure adéquation des stocks aux besoins des clients. Les niveaux de services peuvent être significativement améliorés. Dans un exemple portant sur un cas réel, les délais de livraison des pièces détachés ont été réduits de 30% et les stocks de 10%.
Cas numéro 6 : Accélérer le processus de clôture des comptes
La pression des marchés et des nouvelles exigences réglementaires poussent à plus de vélocité et de transparence dans la publication périodique des résultats financiers. Lorsque qu’il faut assurer la consolidation d’activités réparties sur de nombreux sites, l’absence d'une vision détaillée de ces activités peut conduire à des surprises et des travaux lourds en fin mois. En revanche, si les transactions gérées dans le ou les ERP sont intégrées toutes les heures dans un entrepôt de données d’entreprise, cela permet une pré-validation virtuelle des comptes, ainsi qu’une anticipation des difficultés, et donc une clôture plus rapide. Dans un cas concret, une telle approche a permis de réduire les effectifs affectés à la consolidation, tout en ramenant le délai de clôture de 14 à 7 jours, en permettant d’initier des actions correctrices avant la fin du mois et en limitant sérieusement les surprises.
Pour aller plus loin sur le sujet vous pouvez utilement consulter les liens suivants :
http://www.teradata.com/manufacturing-industry-solutions
http://www.bearingpoint.fr/content/solutions/index_6144.htm
Les industries manufacturières offrent de nombreux exemples de processus et domaines d’application dans lesquels une telle intelligence active peut apporter des avantages significatifs pour la conduite des opérations, comme l’illustrent les quelques cas réels détaillés ci-dessous : gestion des commandes, de la prise d’ordre à la livraison ; planification de la demande ; optimisation des transports ; gestion des garanties ; gestion des pièces détachées ; consolidation et publication des résultats financiers.
Cas numéro 1 : Garantir une efficacité totale du processus allant de la prise de commandes à la livraison chez un fabricant d’articles de sport
Pour cela il fallait parvenir à accélérer les sous-processus et les flux de données associés tout au long de la chaîne du processus global, du centre d'appel, à la logistique, en passant par la fabrication. Le problème rencontré provenait de l’existence d’un ensemble de systèmes hétérogènes, plus ou moins intégrés, ce qui avait pour résultat un délai de six semaines de la commande à la livraison. La solution a consisté à mettre en place une base commune pour traiter l’ensemble des données nécessaires à la fois aux activités opérationnelles et décisionnelles. Cette architecture a permis de ramener de 6 semaines à 48 heures le traitement de 3000 commandes/jour, et d’optimiser dynamiquement les stocks et la production. Cette base de données satisfait près de 2 Millions de requêtes par jour, ceci incluant le suivi de la situation des commandes par les clients via le web.
Cas numéro 2 : Optimiser la planification de production en fonction de la demande
Les planifications type APS (Advanced Planning & Scheduling) sont établies de façon mensuelle ou hebdomadaire. Dans ces conditions, trop souvent les prévisions de production ne sont pas en phase avec la demande réelle, et au final il peut y avoir selon les produits trop ou pas assez de stock. Les difficultés habituelles viennent du manque de fraîcheur des données prises en compte à tous les niveaux de la chaîne, du délai de calcul des différents plans, qui aboutissent à un taux de 35% de prévisions erronées. La solution consiste à réaliser des Plans plus fréquents en s’appuyant à la fois sur des informations historiques des années antérieures et des données fraîches du jour de la situation réelle des commandes, des stocks, des livraisons, des plannings des promotions etc. Le système doit être à même de re-planifier en quelques heures, dés que des variations importantes se produisent, grâce à des pré-alertes sur les dérives par rapport aux plans. Dans les grandes entreprises l'amélioration du processus de planification met en jeu des millions d’euros en terme de réduction des stocks et de réduction des ventes perdues, sans compter l’accroissement de la satisfaction clients qui trouvent leurs produits en rayon ou sont livrés en temps et en heure.
Cas numéro 3 : Optimiser l’utilisation des capacités de transport
Une mauvaise utilisation des capacités de transport peut générer une perte financière non négligeable. Dans la plupart des cas, ces pertes sont liées à planification défectueuse de l’utilisation et du chargement des camions. Ces défauts de planification proviennent d’une qualité insuffisante des informations, d’un automatisation trop partielle des règles de rotation et chargement des camions, ou à une faiblesse des procédures. Dans tous les cas, la connaissance instantanée de la situation de chaque véhicule est nécessaire à l’optimisation des rotations, des trajets et des chargements. La solution consiste à automatiser les plans de chargement, et grâce à des données précises et détaillées permettant de disposer d’alertes en temps réel et de plans dynamiques, les chargeurs de dock maximisent l'utilisation de la capacité de leurs camions.
Cas numéro 4 : Limiter les réclamations frauduleuses en matière de garantie
Au niveau de la gestion des garanties les constructeurs d'automobiles veulent réduire la quantité de réclamations frauduleuses instruites et payées. L’un des principaux problèmes tient au fait que 85% des données de garantie se présentent sous la forme de textes non structurés et sont donc peu pris en compte dans le processus de décision. La solution consiste à intégrer dans un entrepôt de données d’entreprise les textes structurés ou non structurés avec les données opérationnelles et historiques, et à partir de cet ensemble et via des modélisations prédictives, traquer les réclamations frauduleuses. Ce dispositif permet d’être très réactif face aux nouvelles pratiques frauduleuses et de savoir les identifiées avant qu’elles ne prennent de l’ampleur. Une telle approche permet d’améliorer la rentabilité en faisant baisser significativement le coût des réclamations frauduleuses.
Cas numéro 5 : Améliorer la distribution de pièces détachées
Les clients sont insatisfaits quand les pièces détachées dont ils ont besoin ne sont pas disponibles, mais le stockage de pièces qui ne sont pas demandées coûte cher. En fait la satisfaction des clients dépend en grande partie de la connaissance en temps réel de l’état des stocks et des possibilités de livraison à travers la chaîne d'approvisionnement. Ainsi grâce à l’utilisation d’un entrepôt de données d’entreprise il est possible d’obtenir une visibilité de bout en bout de l’ensemble de la chaîne. Et de disposer de prévisions, et d’alertes proactives, ainsi que d’une gestion dynamique des priorités (par exemple quels camions décharger en premier) qui permettent une meilleure adéquation des stocks aux besoins des clients. Les niveaux de services peuvent être significativement améliorés. Dans un exemple portant sur un cas réel, les délais de livraison des pièces détachés ont été réduits de 30% et les stocks de 10%.
Cas numéro 6 : Accélérer le processus de clôture des comptes
La pression des marchés et des nouvelles exigences réglementaires poussent à plus de vélocité et de transparence dans la publication périodique des résultats financiers. Lorsque qu’il faut assurer la consolidation d’activités réparties sur de nombreux sites, l’absence d'une vision détaillée de ces activités peut conduire à des surprises et des travaux lourds en fin mois. En revanche, si les transactions gérées dans le ou les ERP sont intégrées toutes les heures dans un entrepôt de données d’entreprise, cela permet une pré-validation virtuelle des comptes, ainsi qu’une anticipation des difficultés, et donc une clôture plus rapide. Dans un cas concret, une telle approche a permis de réduire les effectifs affectés à la consolidation, tout en ramenant le délai de clôture de 14 à 7 jours, en permettant d’initier des actions correctrices avant la fin du mois et en limitant sérieusement les surprises.
Pour aller plus loin sur le sujet vous pouvez utilement consulter les liens suivants :
http://www.teradata.com/manufacturing-industry-solutions
http://www.bearingpoint.fr/content/solutions/index_6144.htm
Autres articles
-
Teradata nomme Louis Landry au poste de Chief Technology Officer
-
Teradata AI Unlimited pour Microsoft Fabric est désormais disponible en avant-première via Microsoft Fabric Workload Hub
-
Teradata facilite l’application concrète de l’IA générative et accélère la création de valeur pour les entreprises
-
Teradata propose des capacités d’IA exceptionnelles pour les grandes entreprises et les environnements hybrides en collaboration avec NVIDIA
-
Les nouvelles fonctionnalités de ClearScape Analytics maximisent le retour sur investissement en matière d’IA/ML et renforcent la productivité de la data science